|
Crane
maintenance is a specialised job, which is best left to the experts
in the field.
Extracts taken from Industrial Maintenance & Engineering; reported
by Alex von Stempel, editor of Bulk Materials International.
|
The
last thing a busy plant operator can afford is production being interrupted
due to crane or hoist failure. Where cranes are process-critical,
two hours can be a lifetime. Unscheduled downtime is what can cost
a production manager a lot of money. Common types of failure occur
when load ropes are cut or twisted due to shock loading or simply
fatigue. Often this is only the beginning and the result - particularly
with modern cranes, which tend to have tighter tolerances - can be
costly. Damage to electrical cables or contacts is another cause of
concern. As cables are bent forwards and backwards, fatigue sets in.
This can lead to brake failure or a crane motor being put out of action.
|
|
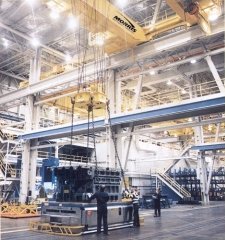 |
Boom or bust
Typically, in good times plant operators are more inclined to spend
money on maintaining cranes and hoists than in bad times when some
of them tend to scrimp and save. "What these operators may not realise
is that when the good times come around again, they will not be
able to work as efficiently as their competitors" says John Lloyd,
Business Development Manager at Morris Material Handling. In extreme
circumstances some equipment can even become dangerous.
Pressures
on the manufacturing sector in the UK have become more acute. In
the past, factories in the UK and elsewhere were shut down for up
to a fortnight and maintenance teams were able to perform the necessary
repairs during that time. This, of course, is no longer the case.
Today many companies, including smaller ones, tend to operate skeleton
crews to keep production going most of the time. Bigger customers
tend to be better, simply because of the rigours of just-in-time
manufacturing. However, production rate and equipment utilisation
changes also mean that maintenance regimes have to be readjusted.
Specialised maintenance service providers now have to work out when
they can fit a service into their customer's busy production schedules.
Technical support 24 hours a day, 365 days a year, with work fully
guaranteed is fast becoming maintenance service industry standard.
|
Outsourcing
Meanwhile a growing number of companies have outsourced their maintenance
departments in order to save cost and space. As a result, they are
benefiting from reduced stock levels and have been able to substitute
a fixed cost (of operating an in-house maintenance department) for
a variable cost.
From a customer's point of view, the value/price of maintenance service
after outsourcing must be higher than the original cost of service
when performed in-house. However, when calculated across crane lifetime
costs, including lost opportunity costs for in-house resourcing, the
savings by subcontracting to a specialist become clearer, specially,
if those specialists provide performance guarantees.
Clearly, every customer wants to feel that he is unique and as M&R
functions continue to be outsourced, industrial plant operators are
beginning to realise that different maintenance service providers
offer different things.
|
|
 |
Wealth
of experience
Morris Material Handling, which emerged as an independent company
following a successful Management Buy Out of the business from receivership
earlier this year, is the largest UK based manufacturer of cranes
and hoists. It has had seven years of experience in providing maintenance
service in the UK and has a network of 13 Material Handling Centres
(MHCs) nation wide, in addition to over 200 independent distributors.
The MHCs together employ approximately 100 staff, including many skilled
technicians and "the company is growing," says Lloyd. Two new Centres
have recently been opened in Cumbria and North West London.
"We maintain cranes that are up to 70 years old," says Roy Humpherson,
one of Morris' regional managers. The MHCs operate hand-in-glove with
Morris Parts Division, which gives them access to a number of unique
services. The most important of these being Allparts and the Swift
Order Shop (SOS). Allparts mission is to supply parts quickly for
any crane, irrespective of its manufacturer. The SOS shop is a separate
part of Morris's manufacturing facility for making urgently needed
parts. When a part is needed for a breakdown, if necessary, the SOS
shop works 24 hours a day to product it. "With this backup our technicians
can go to |
 |
|
site knowing
that they can service any make of crane and obtain or manufacture
almost any part they need" said Lloyd. Morris has recently won several
significant maintenance contracts with major companies such as Corus,
Hewdens and Infraco Sub-Surface Ltd (London Underground). Morris also
services cranes all over the world, including the Far East, the Middle
East and the Caribbean. It recently won a large maintenance contract
with Alstom to maintain cranes in Taiwan.
Morris offers a tiered service approach. The company can provide anything
from an annual inspection service, to a structured service agreement
whereby repairs to certain levels are automatically guaranteed. Morris's
unique all-inclusive Total Crane Care Package is designed to keep
critical production cranes running for a fixed monthly amount with
no surprises. |
 |
 |
 |
|
|